目前我国燃煤发电在电力总装机量中仍占据主要地位,随着全社会对环境问题的日益重视,燃煤电厂的节能减排工作也面临着更高的要求。《煤电节能减排升级与改造行动计划(2014-2020年)》明确提出现役燃煤机组到2020年供电煤耗要达到310g/kWh,大气污染物排放浓度达到燃气轮机组排放限值(即在基准氧含量6%条件下,烟尘、二氧化硫、氮氧化物排放浓度分别不高于10、35、50mg/m3)。对于在役机组尤其是中小型机组,如何实现以上目标需要进行全面深入的分析论证,针对不同机组自身特点制定经济合理的方案并加以科学实施,才有可能达到既定目标。
某厂地处东部地区城区位置,配备了上海锅炉厂(有限)公司生产的高温高压循环流化床锅炉,锅炉型号SG-240/9.8-M257。锅炉采用岛式半露天布置、全钢结构、支吊结合固定、单锅筒自然循环、集中下降管、平衡通风、绝热式旋风气固分离器、循环流化床燃烧方式、后烟井内布置对流受热面。燃烧系统由风帽布风装置、旋风分离器、U型回料阀、床下点火等系统组成。脱硝采用SNCR工艺,还原剂为尿素;脱硫采用炉后石灰石石膏湿法脱硫协同除尘工艺。
燃料市场影响,目前锅炉实际燃烧煤种与设计偏差较大,长期以烟煤、褐煤混煤为主,总体表现为入炉煤挥发份高(30%~45%),灰份较低(15%~25%);其次,由于机组投运时间较长,机组设备老化,中心筒严重变形,风帽磨损加剧。这给循环流化床锅炉的运行和环保排放带来较多问题:
(1)由于入炉煤灰分低于设计值,且中心筒变形严重,分离器效率下降,因此炉内无法形成足够的循环物料,进而导致炉膛内床上热量无法被充分携带到中上部进行换热,因此锅炉运行参数难控制,工况较差,运行风量偏大,氧量高,平均床温达970℃,带高负荷困难;
(2)床温过高导致NOx原始排放浓度升高,最高可达400mg/Nm3,脱硝还原剂耗量大;
(3)风帽形式老旧,风室漏渣现象时有发生,检修更换频次高、更换量大。上述问题严重影响了锅炉的安全稳定运行,导致以上问题原因是锅炉本体存在缺陷且关键部件设计不合理,因此委托中国华能集团清洁能源技术研究院针对锅炉现有问题制定了技改方案并加以实施。
循环流化床锅炉运行中需要建立起稳定的物料循环,风帽对于实现这一过程具有重要意义。锅炉设计时必须保证空气均匀地分布在整个炉膛截面上,使得物料均匀流化,避免出现流化死区,防止出现风室漏渣、流化不均、结焦等事故。
锅炉原有风帽为钟罩式风帽加直通式芯管组合,风帽外罩开孔8个,外罩与芯管采用焊接连接,外罩材质ZGCr26Ni4Mn3NRe,芯管材质1Cr18Ni9Ti,具体结构如图2所示。实际使用中,尽管对冲安装布置,但由于小孔为水平方向,加入床料后,部分灰渣进入芯管与外罩间隙,外罩小孔的出风量会有不同程度变化,对冲效果大打折扣,相邻风帽间冲刷严重。风帽外罩磨穿后,大量床料漏至风室,影响锅炉安全运行。
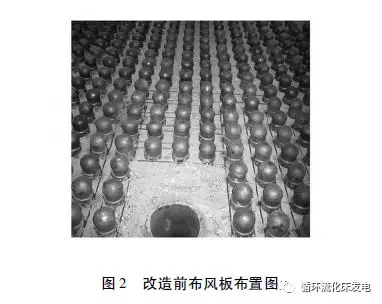
针对原风帽型式和材质存在的问题,从风帽的组合形式、固定方式方面入手,对布风装置芯管、风帽结构进行全面优化。对比原风帽,新型风帽外罩出风小孔向下倾斜20°,加厚了出风小孔外罩,减少相邻风帽的扰动和床料反窜,采用铸造加工,外罩材质升级为ZG40Cr25Ni20,提高耐磨性和使用寿命。芯管由直通式改为四周出风,上部端板与风帽焊接固定,防止风帽脱落从芯管漏渣。
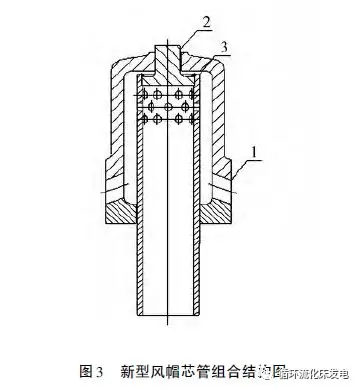
旋风分离器是循环流化床锅炉的关键部件,其主要作用是将大量高温固体物料分离出来送回炉膛,以维持炉膛循环流化运行,保证燃料和脱硫剂多次循环。锅炉原有旋风分离器筒体直径5408mm,进口截面4828×2028mm,中心筒直径1912mm,插入深度2900mm。分离器中心筒由上下两个筒体组成,上部筒体由12片扇形长板拼接而成,下部筒体为整圆设计,材质为1Cr20Ni14Si2,厚度6mm。受到锅炉启停及中心筒区域温度较高的影响,上部筒体扇形长板之间原有的拼接缝逐渐演变成为裂隙,加之扇形长板彼此之间膨胀不均,变形严重,裂隙逐步加大,宽度达到50~200mm,如图4所示。
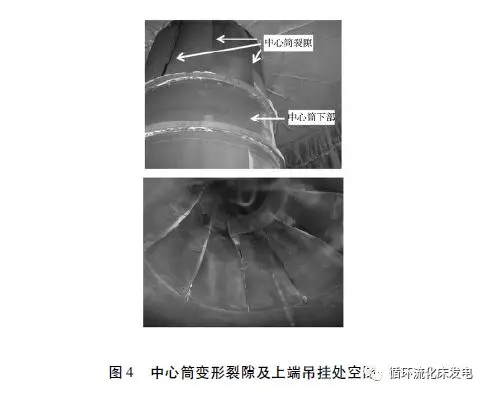
中心筒的吊挂为拉筋吊挂,中心筒上端的每片扇形板由拉筋将筒体与分离器外护板焊接固定。在中心筒受热膨胀、受冷收缩时,拉筋与中心筒焊接处胀缩受阻,胀缩顶拉力会使中心筒上部产生严重变形,露出巨大空隙。由于中心筒裂隙和上部空隙的存在,造成烟气短路。通过对取得的飞灰样分析发现,锅炉分离器的分离效果不佳,相当数量的飞灰无法有效分离下来,飞灰中位粒径d50=39.88μm。
针对现存问题,采用中心筒偏置、变径结构,筒体采用Cr25Ni20MoMnSiNRe整体铸造,为增强机械强度,筒身厚度由6mm提升至16mm。通过增加分离器进口耐磨料层的厚度,减少进口面积增大进口烟气流速来提高分离效率,增加凸台缩口后进入分离器入口烟气流速由原来的20m/s增加到24m/s。
采用自由吊挂式安装,借助原旋风筒环形槽钢,在环形槽钢上焊16个支架,中心筒通过上部大筋板安放在16个支架上,中心筒与支架间自由配合,可相对滑动。由于大筋板、三角筋板和中心筒为一体铸造,具有较高的强度,有效避免中心筒在运行中易受胀缩应力而变形成椭圆的问题。为了保证密封,在筒体上端密封浇注料底部加一圈密封环板,用岩棉把筒体与浇注料缝隙塞满后,焊接一圈密封环板,有效的防止烟气短路问题。
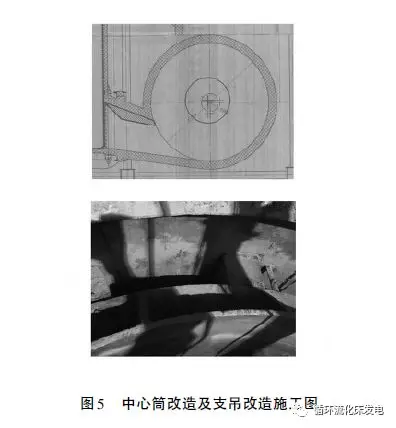
锅炉改造后,由于分离器入口烟气速度上升,中心筒插入深度及结构得以优化,使得旋风分离器效率大幅提升,因此炉内循环灰量显著增加,炉内换热效率改善,床温可控性提高,NOx原始排放浓度相较改造前能够有所下降。而布风装置改造后,布风板阻力恢复到设计值,布风均匀性提升,因此一次风量下降,风机耗电量降低。以下为各运行参数改造前后对比:
(1)锅炉各项运行参数恢复正常,一次风量下降30%,平均床温下降了40℃。
(2)分离器效率明显提升,飞灰中位粒径d50由39.88μm降至16.6μm。
(3)一次风机和引风机电耗下降约10%,排烟损失和固体不完全燃烧损失降低,锅炉效率较改造前提高了1.22%。
(4)氮氧化物生成浓度得到有效控制,满负荷工况小于180mg/Nm3(6%O2,标态),SNCR脱硝还原剂耗量大幅下降,脱硝后排放浓度小于50mg/Nm3。炉膛上部温度提升明显,特别是SNCR反应区温度,在50%~100%负荷下区域温度基本能保持在800℃以上,能够有效保证低负荷的脱硝效率。
通过节能环保一体化改造妥善解决了循环流化床锅炉存在的诸多问题,各项运行指标回归正常,更为关键的是在环保方面通过有效降低氮氧化物原始生成浓度,提升锅炉低负荷脱硝效率,使得SNCR脱硝后NOx排放最终达到50mg/Nm3的超低排放标准。这一改造技术的成功实施验证了锅炉节能环保一体化改造的可行性,为循环流化床锅炉尤其是中小型锅炉实现节能环保的同步达标提供了有益的借鉴。 |